- MAAG
- / Gears
- / Gears for horizontal mills /
- MAAG® GEAR Girth Gear
MAAG® GEAR Girth Gear
Keep your mill or kiln up and running with our heavy-duty girth gears. Heavy-duty comminution requires heavy-duty equipment – and our MAAG® GEAR Girth Gears are up to the task. Manufactured using state-of-the-art processes and high-quality source materials, our line of girth gears is fit-for-purpose and for a lifetime – ensuring long-lasting, high-performance for your mill or kiln.
Our girth gears let you get the best from your mill or kiln
Our comprehensive expertise in forged gear ring technology comes from our more than 50 years of experience, as well as our collaborations with leading mill suppliers and technical universities. As a member of the American Gear Manufacturers Association (AGMA), we are actively involved in defining the standards for gear-rating calculations, service factors and other design standards. We continuously invest in technology and knowledge – along with steadily strengthening our network of partners.
Over 1,000 MAAG® GEAR Girth Gears are in service around the world – delivering optimal reliability for the cement and mineral industries. Applications for our girth gears also extend into the chemical processing and ceramic industries, food processing and pulp and paper.

Remarkable raw materials
We build our fabricated girth gears using forged gear rim material and bodies made in an electro-welded structure. Compared to girth gears with cast base material, the manufacturing process is more sophisticated, as well as more reliable. The uniform and homogenous crystal structure of the forged rims, guarantees identical material properties throughout the entire toothing. Casting defects like hot tears, porosity or shrinkage are excluded – resulting in a stronger and more reliable girth gear.
When supplying ductile cast iron or cast-iron girth gears, we source the raw material from world-leading foundries – working closely with them to ensure the highest quality.
Manufactured for high-performance
Our cutting-edge production method ensures that our girth gears deliver optimal power and stable operation for your mill or kiln, along with high wear resistance and long operating time. There are five steps to our manufacturing process for fabricated girth gears, including strict quality checks after the final welding and tooth cutting:
To start, high-grade material is rolled and forged to the required ring dimension. Web, rips and junction plates are welded to the forged rim material according to specific qualified processes. Components undergo strict non-destructive tests, followed by post-weld heat treatment. Rough and finish cuttings trim the girth gear to its final dimension. Finally, the tooth geometry, run outs, hardness and many other properties are measured and documented as part of the closing inspection.

Made for your requirements today and tomorrow
Working to your precise needs, our highly-experienced engineers use the latest finite elements modelling software to design and engineer girth gears that fit your specifications. Our modern production sites and continuous advancements ensure that our MAAG® GEAR Girth Gears meet your needs now – and into the future.
Long-lasting, heavy-duty girth gears
Expert customisations
No risk of inclusions and other irregularities
Well-thought-out, well-produced girth gears for your mill or kiln
The strength of our heavy-duty MAAG® GEAR Girth Gears comes from the strength of our source materials and manufacturing process. We use fabricated steel, forged rings, rolled plates and ductile (nodular) cast iron to ensure the smooth operations for your mill or kiln. The continuous investment in our modern machine shops guarantees state-of-the-art girth gear production, in a wide-range of sizing:
External gears: Maximum diameter: 11,200 mm; Face width: 1,250 mm; Maximum module: 45 by hobbing
Internal gears: Maximum diameter: 6,500 mm; Face width: 400 mm; Maximum module: 25.4
The precision and quality of the girth gear manufacturing process ensures accurate alignment – resulting in heavy-duty gears that keep your comminution equipment running smoothly now and in the future.
The complete drive system
Ball and grinding mills, kilns and dryers are all operated with girth gears – but the girth gear is only one part of the power train. Taking into account the requirements of your application, available space and other individual parameters, our girth gears power your equipment together with pinions and intermediate gear units, lateral gear drives or, in the case of the MAAG® GEAR MAX Drive, with two spur gear drive units.
The classic open gear arrangement includes the main motor, an intermediate gear unit for speed reduction and the pinion, which meshes with the girth gear. Our standardised product range and individually-designed girth gears and pinions allow us to supply a customised power train – purpose-built for your specific application.
If you have higher power needs and limited space, our MAAG® GEAR LGDX lateral gear drive is the preferred solution. The symmetrical casing of our LGDX gear drive gives you high flexibility with positioning – letting you install the drive train at the best location within your mill. By delivering the lateral gear drive together with the girth gear, we ensure that both components match perfectly.
Our girth gears have a key role in meeting the highest power demands in vertical rollers mills. The MAX Drive powers vertical roller mills up to 15,000 kW with two spur gear drive units that mesh with the girth gear under the mill table.

Backed by experience and know-how
While our modern manufacturing processes are impressive, it’s really our highly-skilled engineers and operators who make our girth gears stellar. Our engineers and machine operators are trained in sophisticated engineering software, allowing them to meet your precise specifications by creating high-quality girth gears made from a variety of materials. Depending on your needs, we can manufacture all geared components of the entire power train or individual components.
Based on engineering analysis and many years of experience, we can also propose design improvements to increase part reliability – delivering smooth operations for your mill or kiln long into the future.
Downloads
MAAG® Open gears
PDF (1.63 MB)
Condition Monitoring Systems
PDF (0.66 MB)
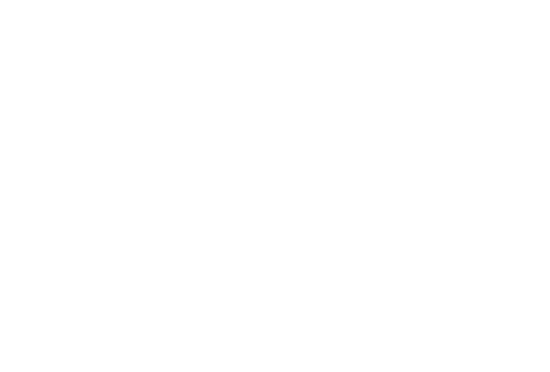
Join our newsletter.
Don’t miss out on the latest news, updates,
and insights - from MAAG.
© copyright MAAG Gear 2025. All rights reserved.
MAAG GEAR
INDUSTRIES
SERVICE CENTER
INDUSTRIES
SERVICE CENTER