- MAAG
- / Gears
- / Gears for horizontal mills /
- MAAG® GEAR WA / Temperex Gear
MAAG® GEAR WA / Temperex Gear
Crush your grinding challenges with our single and multistage gear units. Designed to drive comminution machinery in minerals processing, our MAAG® GEAR WA and Temperex Gearbox delivers impressive performance and reliability for your horizonal mill. The single stage MAAG® GEAR WA and multistage MAAG® GEAR Temperex Speed Reducers meet your crushing needs rationally and economically.
Reliable comminution speed reducer gear unit for your horizontal mill
Drawing on more than 100 years of experience with heavy-duty industrial gear units and state-of-the-art manufacturing processes and calculation methods, our MAAG® GEAR WA / Temperex gear unit brings impressive performance and reliability to your horizonal mill. A parallel cylindrical wheel speed reducer gear unit, our single stage MAAG® GEAR WA and the multistage MAAG® GEAR Temperex meet your precise needs for comminution or other applications.
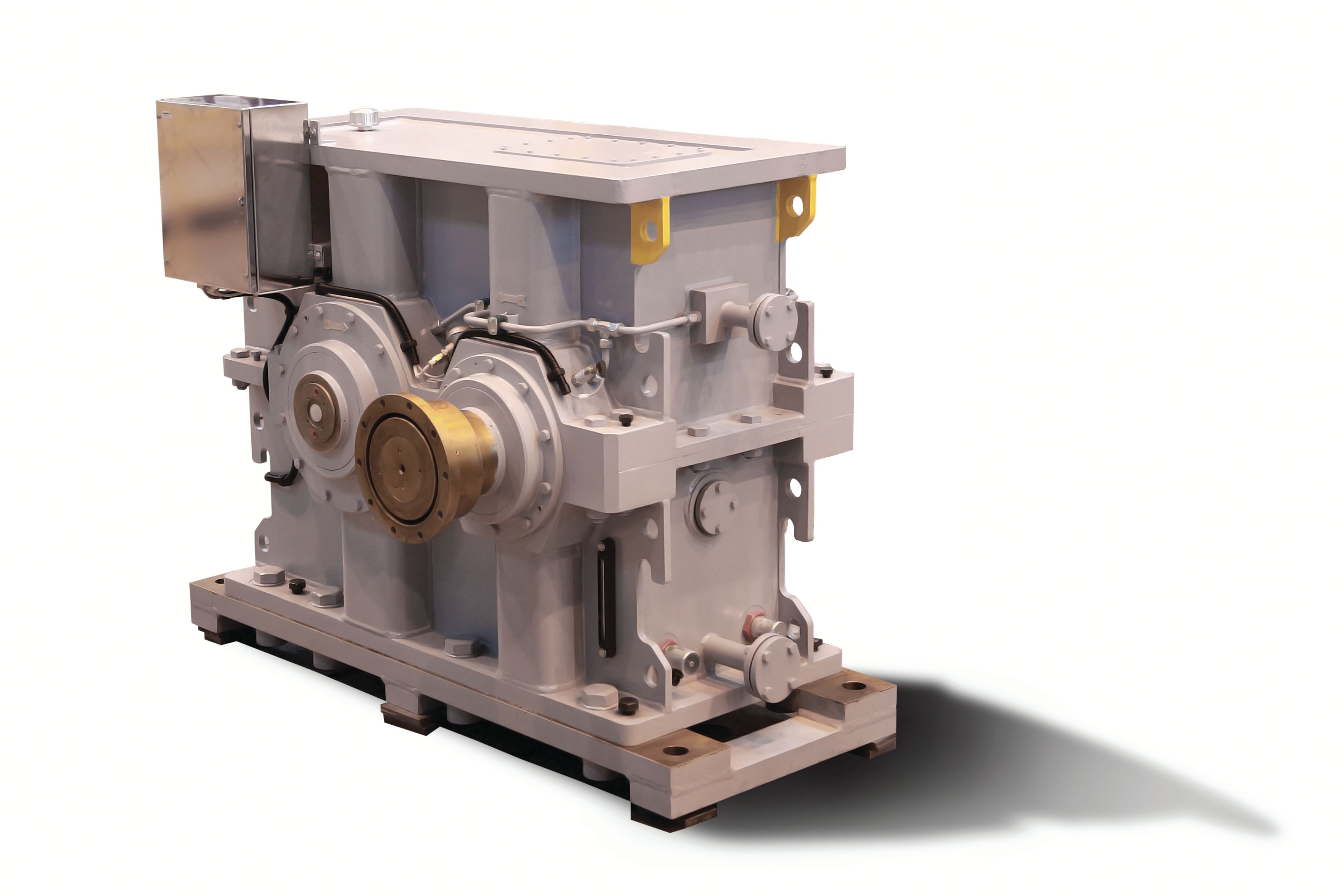
Consistent drive for crushing, adapted to your requirements
We designed the MAAG® GEAR WA / Temperex Gear Units specifically for driving comminution machinery in minerals processing. These single and multistage gear units effectively transmit torque from electric driver motors to ball, rod, SAG, AG or other types of horizonal mills – giving you dependable power output that works in your heavy-duty application.
With the potential to accommodate the widest possible range of requirements, the broad scope and modular design of the MAAG® GEAR WA / Temperex Gear Unit ensure that you get the crushing solution that perfectly fits your application and unique circumstances. Beyond the wide range of power and size configurations, we can also deliver other designs on request – and our engineers can work with you to guarantee your solution is adapted to the power you require, as well as the speed of your motor and mill.
The standard version of the MAAG® GEAR WA / Temperex works within an ambient temperature range of -4 °C to +40 °C. We can also adapt the design and installation configuration for other ambient temperature ranges, depending on your needs.
Longevity from the start
Our advanced manufacturing processes ensure the high strength and wear resistance of our MAAG® WA / Temperex gear unit – delivering durability right from the very beginning. Recognising the heavy-duty demands of the mineral processing industry, we make sure our gear units are up to the challenge with the latest developments in heat treatment and teeth machining. And our precise machines and strict control process ensure high-quality production at every step.
The toothed components are produced in-house to the strictest quality standards, using case-hardened and heat-treated steel. This in-house heat treatment gives us complete control over the hardening processes and material properties – and gives you confidence in the long-lasting performance of the MAAG® GEAR WA / Temperex Gear Unit.
The gears in the MAAG® GEAR Temperex range are made of chrome-nickel molybdenum steel and case-hardened and ground on precision tool machines. The modified tooth profiles of the cylindrical helical gears used in our Temerpex Gear Units limit scuffing or scoring – and provide better load distribution.
Proven durability by design and manufacturing
Minimal maintenance and high uptime
Customisable for your individual mill requirements
Gear units designed and built for unfailing speed reduction
The well-manufactured parts and high-quality materials we use for our MAAG® GEAR WA / Temperex Gear Units contribute to their reliable function and simplified maintenance. We also offer upgrades and additional equipment to meet your mineral processing needs.

The complete WA / Temperex mill drive system includes the
motor, gear unit, lubrication system, auxiliary drive, girth gear and pinion.
Top-notch components
The standard installation of the MAAG® GEAR WA / Temperex Gear Unit includes a flexible coupling for the high-speed shaft and a toothed coupling for the low-speed shaft, delivering low vibratory loads in the drive train and a relatively wide range for axial and radial displacement. The couplings have no lubricants that need changing – resulting in reliable virtually maintenance-free operation.
All gear wheels in the WA gear unit are made of case-hardened steel, delivering exceptional wear resistance for the teeth, while allowing light, compact gearbox construction. Our in-house heat treatment and precise teeth machining result in optimal tooth contact under load condition and the toothing of the helical stage includes all necessary modifications to ensure smooth meshing.
Depending on the type of load transmission our WA / Temperex Speed Reducers are equipped with spherical or tapered cylindrical roller bearings. In order to minimise maintenance and keep your horizontal mill running smoothly, the bearings in all of our industrial gear units are covered and protected against dust and other possible contaminations, using a combination of lip and labyrinth seals designed for mineral lube oils.
Straightforward instrumentation
The standard version of our WA / Temperex Gear Unit includes resistance thermometers to monitor the bearings and oil temperature. The instrumentation can be upgraded to a vibration monitoring system as an additional option.
You can upgrade your speed reducer gear unit to allow condition-based preventive maintenance – letting you detect faults at a very early stage and plan future service interventions.
Auxiliary drive for cost-effective maintenance
Fitted behind the electric motor or on the free high-speed shaft end of the gear unit, the auxiliary drive of our MAAG® GEAR WA / Temperex Gear Unit gives you a cost-effective way to perform maintenance. Use the auxiliary drive to simplify build-up welding on your mill or to conveniently re-position the mill during maintenance. Connected to the gearbox or electric motor via an automatic overrunning clutch, the auxiliary drive has a Kirk key interlocking system to prevent it from working simultaneously with the main motor.
Downloads
Condition Monitoring Systems
PDF (0.66 MB)
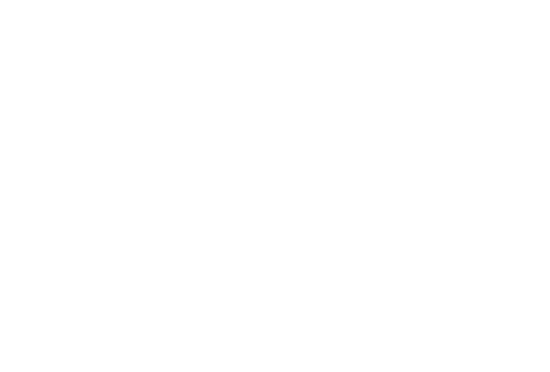
Join our newsletter.
Don’t miss out on the latest news, updates,
and insights - from MAAG.
© copyright MAAG Gear 2025. All rights reserved.
MAAG GEAR
INDUSTRIES
SERVICE CENTER
INDUSTRIES
SERVICE CENTER