- MAAG
- / Gears
- / Gears for vertical roller mills /
- MAAG® GEAR CEM Drive
MAAG® GEAR CEM Drive
Increase the energy efficiency of your vertical roller mill. Reducing energy consumption is a top priority for both environmental and economic reasons. But you can't afford to lose performance in your VRM. Our MAAG® GEAR CEM Drive system achieves both, powering VRMs up to 14 000 kW with a compact integrated motor that reduces power loss by more than 20%.
The most compact drive system for vertical roller mills
Where there’s power, there’s potential. That was the thinking behind the design of the CEM Drive. We knew we could bring down energy consumption and the associated CO2 emissions with some straightforward engineering. And that’s exactly what we’ve achieved. By combining our proven MAAG® planetary gear technology with an innovative electric motor – and removing the bevel stage – we’ve reduced power loss, cut carbon emissions and created a compact drive system that fits in almost any vertical roller mill.

What’s more, we’re also making the most of digital tools to enhance performance and reliability. The IOT-ready CEM Drive can utilise continuous condition monitoring to keep an eye on your drive. With Predicta, our online condition monitoring service, sensors catch the earliest signs of wear and tear, enabling you to react before problems have the chance to develop into events. When you add mySentinel service agreements, you take your maintenance strategy from reactive to proactive – totally eliminating unplanned downtime. Your drive system will never let you down again.
Perfectly sized, with nothing wasted
The modular design of our MAAG® CEM Drive system covers a power range from 4000 to 14 000 kW. The integrated motor eliminates the traditional bevel gear stage, which not only makes the compact configuration possible but also reduces the number of rotating parts and bearings in the entire drive train to an absolute minimum. This simplifies installation and service, and of course reduces maintenance costs.
Because we know that your feed characteristics change, we also wanted to make sure your mill could adapt on the fly. The variable frequency converter that powers the integrated motor enables you to quickly and easily optimise your grinding process for maximum results.
Downsizing the footprint, upgrading the power
Downsizing the motor to fit in the available space of a bevel gear stage was the most challenging part of designing our CEM Drive system. The solution is a permanent magnet synchronous motor with single-tooth stator coils and with direct oil cooling for the stator. The use of permanent magnets minimises resistive losses, giving you reduced energy costs. In combination with the frequency converter, the motor delivers constant torque over a wide speed range, with consistently high efficiency. As a result, we’ve managed to up the capacity of the drive system while reducing the footprint. Now, the size of the drive system depends only on the dimensions of the mill table. The compact size gives the flexibility to use the same CEM Drive for multiple mill sizes, allowing fewer spare gears needed for insurance. This makes the MAAG® CEM Drive an obvious choice for retrofit and upgrade projects, and gives you the possibility to do more with less.
Easily adapts to different material characteristics
Highly energy-efficient operation
IOT-ready for optimised reliability
Compact footprint
A low maintenance drive system – high availability, high reliability
Space-saving design – without compromising function
The integrated motor includes loss-optimised single-tooth coils and a wear-free self-exciting permanent magnet rotor. The self-excited rotors make external excitation devices unnecessary. Together with the embedded magnets, which concentrate the magnetic fields in the integrated motor, this feature contributes to the CEM Drive’s space-saving and low-maintenance design. Furthermore, the single-tooth coil decreases the axial length of the motor and the total amount of copper also reduces corresponding ohmic losses.
Direct oil cooling
The MAAG® CEM Drive uses direct oil cooling, ensuring the integrated motor is completely separated from the dusty environment around the vertical roller mill. This also means that the gear lubrication oil is not contaminated with other cooling media. As the motor cooling requires the same amount of oil as a bevel gear stage, the size of the lubrication system remains the same – giving you more functionality with identical compact dimensions.
Tested-and-true torque transmission
An internal geared coupling transmits the motor torque to the well-proven MAAG® PV gear stage, a double planetary gear stage with torque split. This double planetary configuration has been used successfully in our MAAG® CEM Drive gear unit for many years. It allows for a reduction in both the tooth length and the losses in the second gear stage because it transmits only 75-80% of the torque. The self-centring inner gear ring and sun pinion deliver optimised force flow from the first to the second planetary stage.
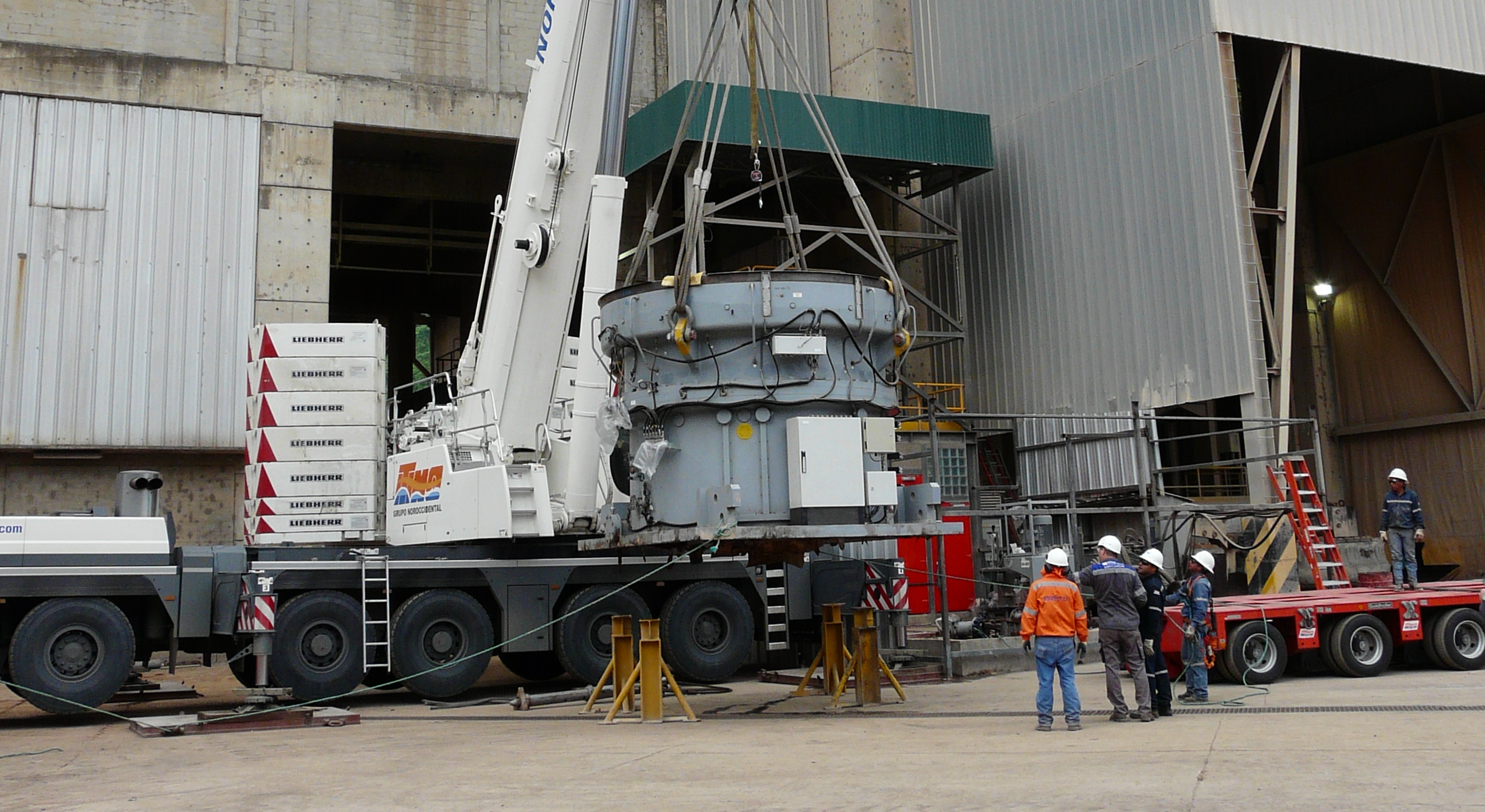
High-performance bearings
The thrust bearing, which supports the mill table of your vertical roller mill, absorbs the static and dynamic loads from the grinding process. Each bearing pad in the MAAG® CEM Drive system is lubricated with high- and low pressure oil and lined with Babbitt metal at the contact surface. The circular, even shape of the casing guarantees an optimal force flow from the mill table into the foundation of your vertical roller mill. Both the gear part and the integrated motor of our MAAG CEM Drive system are equipped with slide bearings. Compared to roller bearings, slide bearings offer higher damping and their unlimited lifespan provides smoother operations and exceptionally high availability for your vertical roller mill.
The MAAG CEM Drive combines proven technology and parts from the IronDrive series with the necessary adjustments to deliver high functionality for vertical roller mills. The standardised design allows you to use the drive unit in all types of mill - optimal for vertical roller mills.
Oil supply unit keeps the gear unit running smoothly
The oil supply units for our vertical roller mill gear units and drive systems includes low-pressure pumps to feed bearings and gears with filtered and cooled lubrication oil. High-pressure pumps supply the oil for the thrust bearing from a separate compartment of the tank filled with chilled and filtered oil from the low-pressure section. Using only clean oil on the high-pressure side allows us to improve the lifespan of pumps and thrust bearing segments.
Downloads
Condition Monitoring Systems
PDF (0.66 MB)
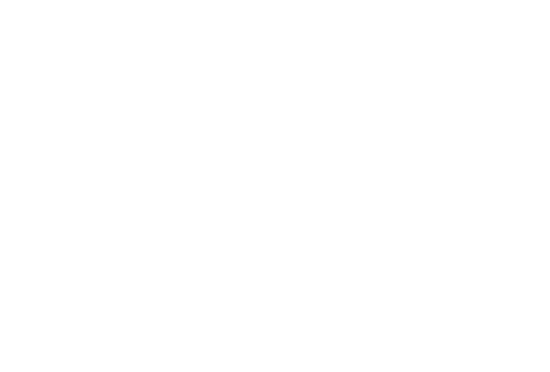
Join our newsletter.
Don’t miss out on the latest news, updates,
and insights - from MAAG.
© copyright MAAG Gear 2025. All rights reserved.
MAAG GEAR
INDUSTRIES
SERVICE CENTER
INDUSTRIES
SERVICE CENTER