Gear up for success: gearbox replacement project in Iraq
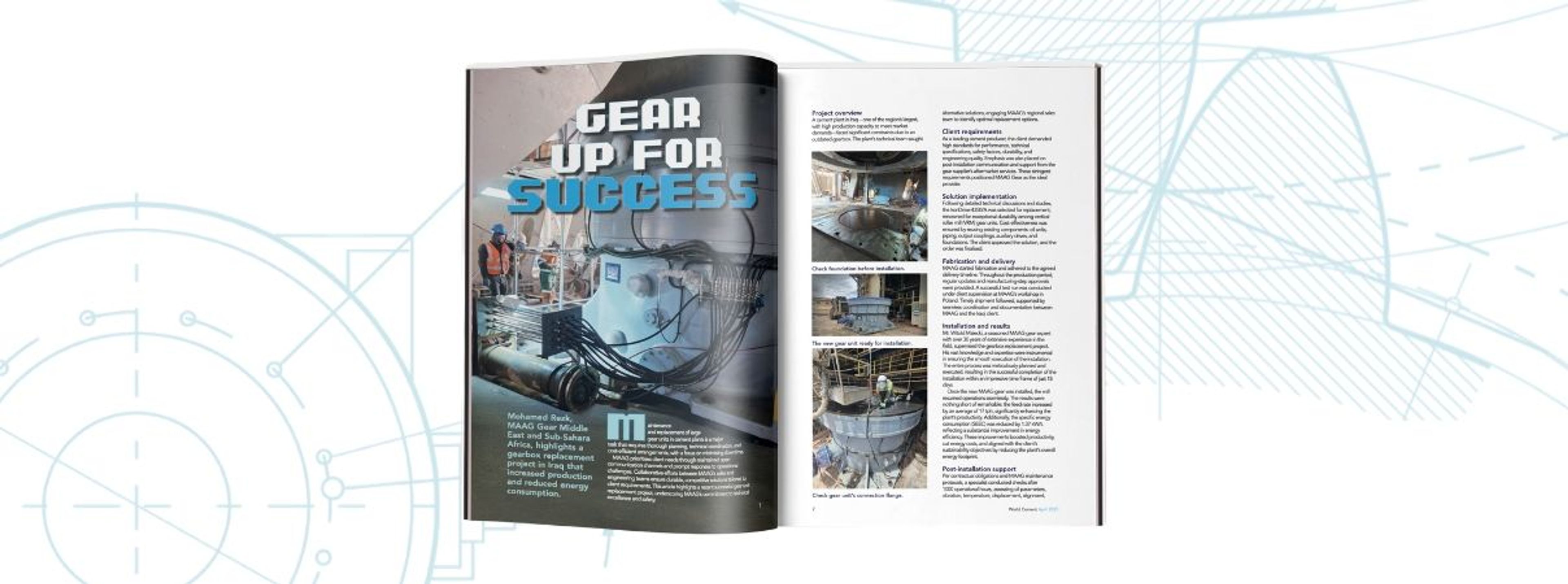
Mohamed Rezk, MAAG Gear Middle East and Sub-Sahara Africa, highlights a gearbox replacement project in Iraq that increased production and reduced energy consumption.
Maintenance and replacement of large gear units
Maintenance and replacement of large gear units in cement plants is a major task that requires thorough planning, technical coordination, and cost-efficient arrangements, with a focus on minimising downtime.
MAAG prioritises client needs through maintained open communication channels and prompt responses to operational challenges. Collaborative efforts between MAAG’s sales and engineering teams ensure durable, competitive solutions tailored to client requirements. This article highlights a recent successful gear unit replacement project, underscoring MAAG’s commitment to technical excellence and safety.
Project overview
A cement plant in Iraq – one of the region’s largest, with high production capacity to meet market demands – faced significant constraints due to an outdated gearbox. The plant’s technical team sought alternative solutions, engaging MAAG’s regional sales team to identify optimal replacement options.
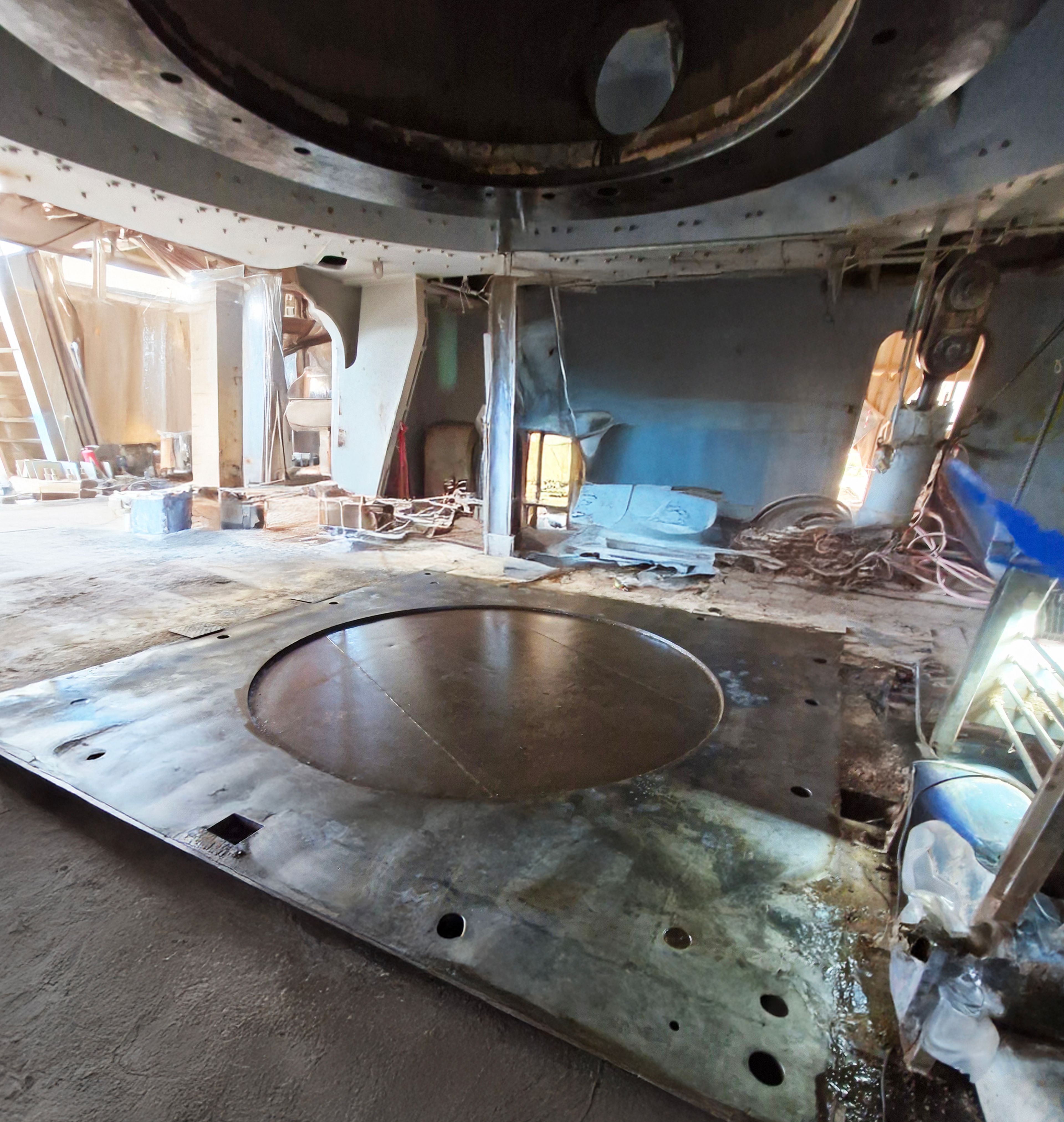
Client requirements
As a leading cement producer, the client demanded high standards for performance, technical specifications, safety factors, durability, and engineering quality. Emphasis was also placed on post-installation communication and support from the gear supplier’s aftermarket services. These stringent requirements positioned MAAG Gear as the ideal provider.
Solution implementation
Following detailed technical discussions and studies, the IronDrive-4350/A was selected for replacement, renowned for exceptional durability among vertical roller mill (VRM) gear units. Cost-effectiveness was ensured by reusing existing components: oil units, piping, output couplings, auxiliary drives, and foundations. The client approved the solution, and the order was finalised.
Fabrication and delivery
MAAG started fabrication and adhered to the agreed delivery timeline. Throughout the production period, regular updates and manufacturing-step approvals were provided. A successful test run was conducted under client supervision at MAAG’s workshop in Poland. Timely shipment followed, supported by seamless coordination and documentation between MAAG and the Iraqi client.
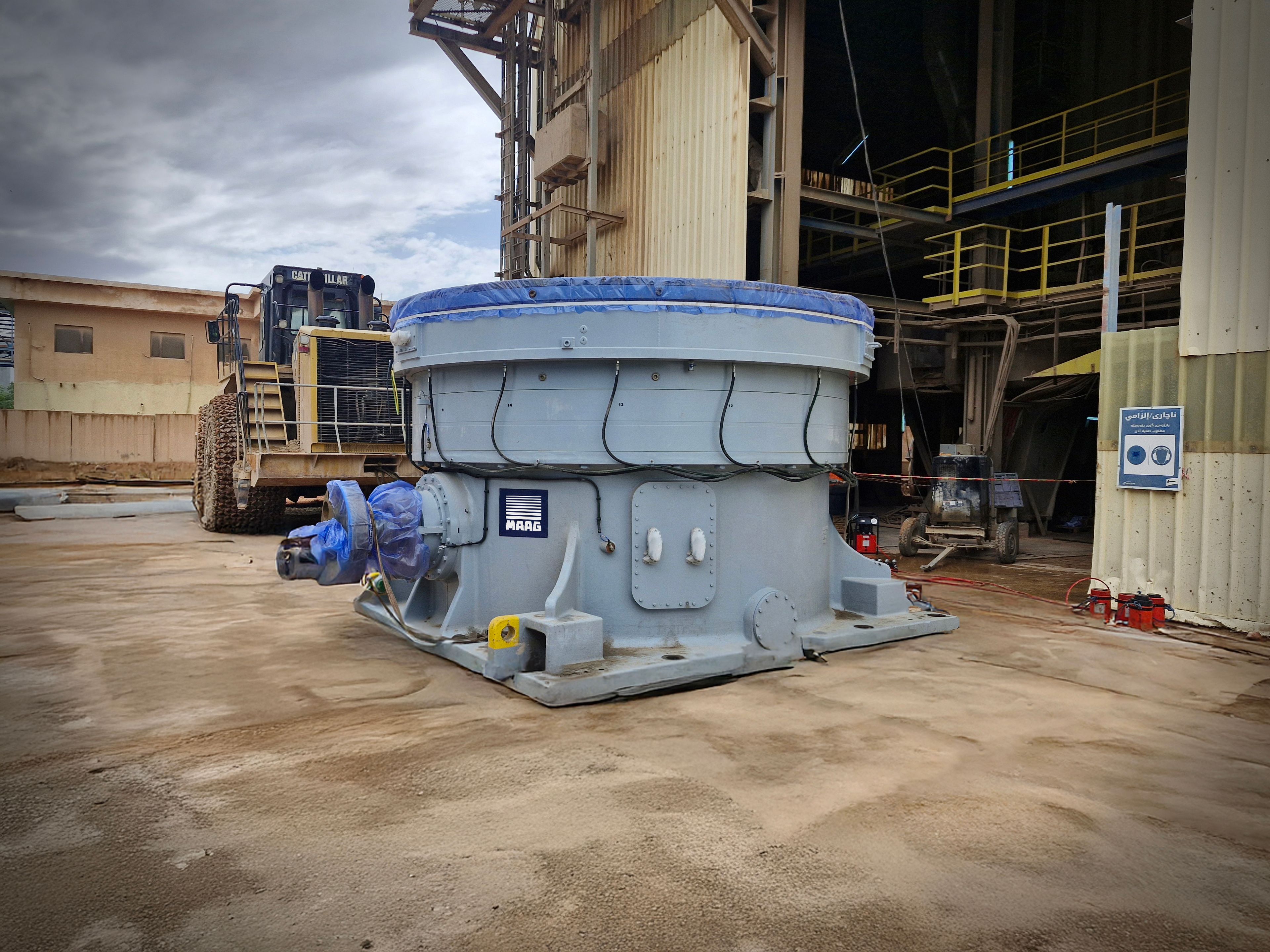
Installation and results
Mr. Witold Malecki, a seasoned MAAG gear expert with over 30 years of extensive experience in the field, supervised the gearbox replacement project. His vast knowledge and expertise were instrumental in ensuring the smooth execution of the installation.
The entire process was meticulously planned and executed, resulting in the successful completion of the installation within an impressive time frame of just 15 days.
Once the new MAAG gear was installed, the mill resumed operations seamlessly. The results were remarkable:
- - Feed rate increased by an average of 17 tph, significantly enhancing productivity.
- - Specific energy consumption (SEEC) reduced by 1.37 kW/t, improving energy efficiency.
These improvements boosted productivity, cut energy costs, and aligned with the client’s sustainability objectives by reducing the plant’s overall energy footprint.
Post-installation support
Per contractual obligations and MAAG maintenance protocols, a specialist conducted checks after 1000 operational hours, assessing oil parameters, vibration, temperature, displacement, alignment and foundation fixation.
All parameters indicated stable performance. Ongoing support is provided by MAAG’s sales and aftermarket teams to address client needs.
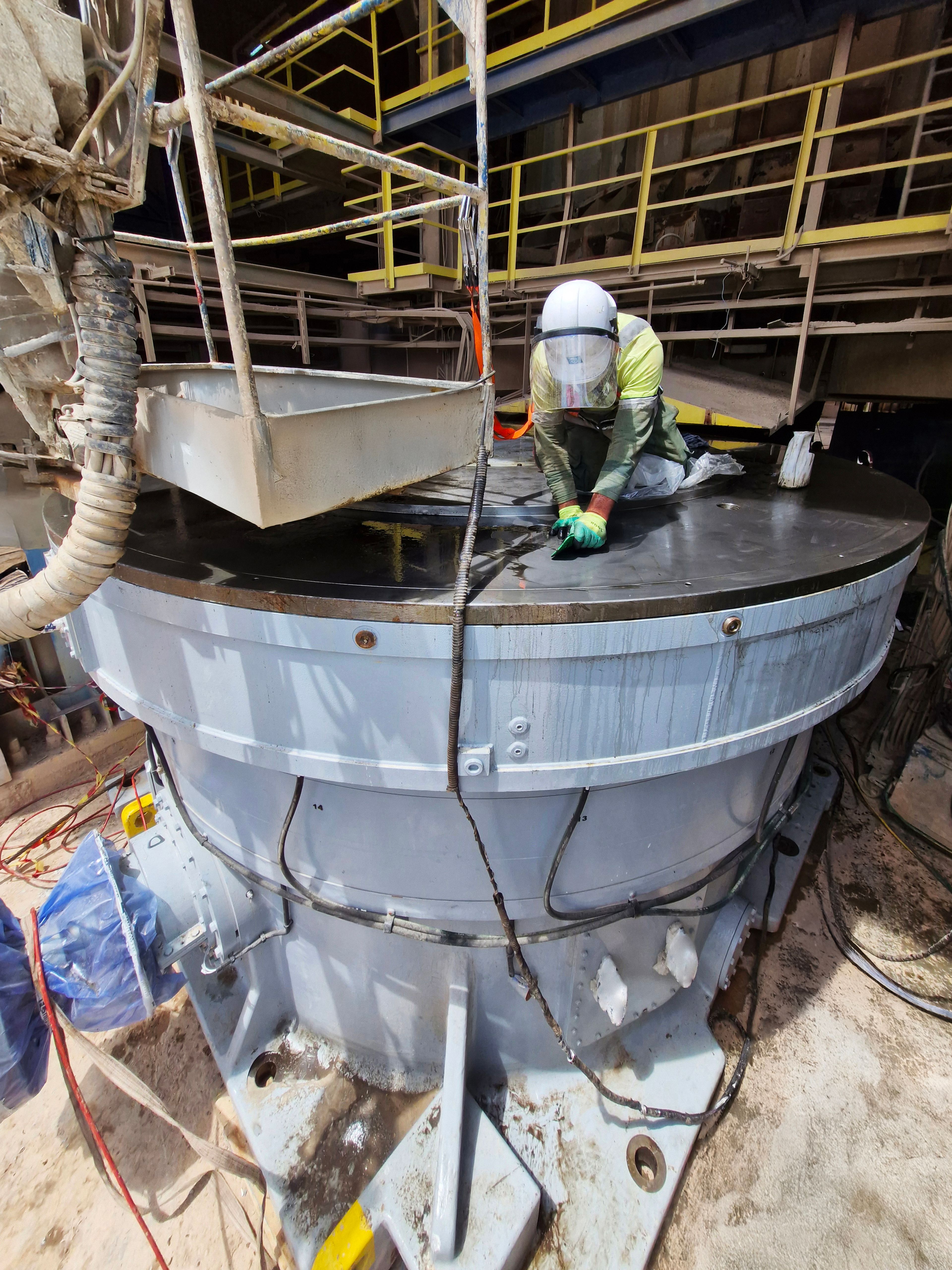
Selection process
MAAG Engineering selects the right design from their wide product range based on specific applications, parameters, and site conditions.
For this project, the 2-stage MAAG Iron Drive was chosen as the most beneficial and reliable solution.
The MAAG Iron Drive series accommodates power ranges from 1500 up to 13000 kW - all in a compact unit. The 2-stage variant features antifriction bearings on bevel and planetary stages (sleeve bearings available on request), while the 3-stage unit uses sleeve bearings throughout. Its circular casing ensures optimal force distribution and flow from mill table to the foundation of the vertical roller mill. The robust gear casing for the MAAG Iron Drive can be executed as fabricated and welded construction or in cast steel.
To absorb shock loads from the grinding process, the axial thrust bearing supporting the mill table is composed of a dozen single tilting thrust pads lined with Babbitt metal at the contact surface. Each pad is lubricated individually by a forced oil circuit. Subject to specific grinding process requirements, the MAAG Iron Drive incorporates a high-pressure lubrication system for hydrostatic table support and is equipped with emergency shoulders to safeguard gears during table tilting.
Key benefits of the MAAG
Iron DriveThe MAAG Iron Drive series benefits from smart design, optimising mill performance and enabling proactive maintenance.
- - Easy access to bevel gearing: achieved via a larger inspection port.
- - Reduced downtime: facilitated during adjustment of bevel gear contact patterns.
Simplified maintenance: the bevel pinion can be removed without dismantling the gear unit from the mill.
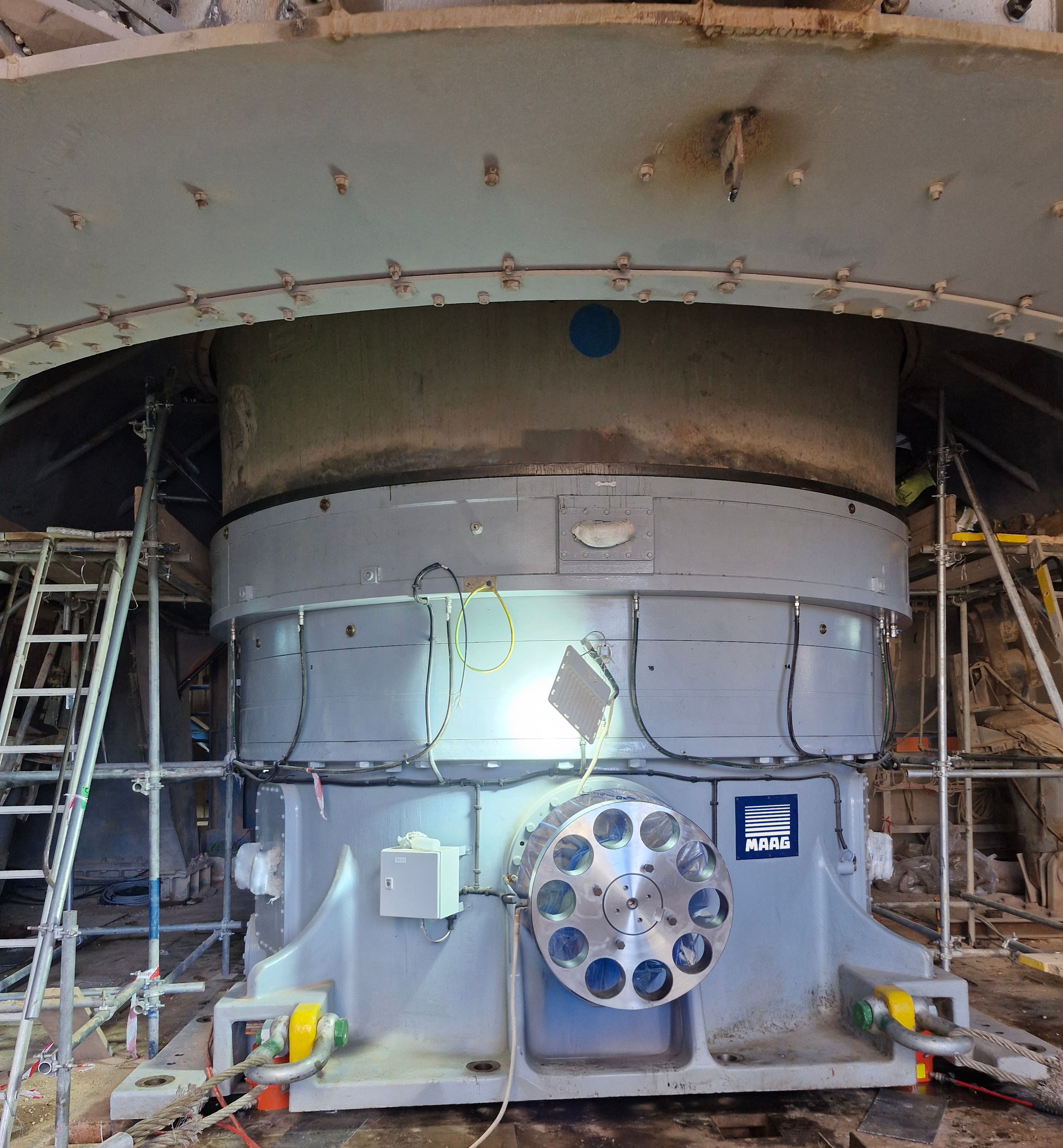
Best practices for client satisfaction
✅ Open communication: clear and consistent communication channels ensure prompt resolution of challenges or concerns.
✅ Collaborative approach: close coordination between sales, engineering teams, and clients delivers durable, competitive solutions tailored to specific needs.
✅ Technical excellence: technical proficiency and safety are prioritised, ensuring adherence to high standards of performance and reliability.
✅ Cost-effectiveness: reuse of existing components, where feasible, guarantees quality without compromising cost efficiency.
✅ Timely delivery: agreed fabrication and delivery timelines are rigorously followed, with continuous client update.
✅ Post-installation support: ongoing maintenance checks and guidance ensure long-term operational success.
✅ Condition monitoring services: advanced monitoring tools enable proactive maintenance planning and prevention of unplanned downtime.
MAAG takes pride in supporting clients to overcome critical bottlenecks, enhancing production efficiency while minimising downtime. Performance improvements, reduced energy consumption, and streamlined operations underscore these achievements.
MAAG operates as a unified team with a singular focus: guaranteeing client success.
(Article published in World Cement Magazine, 2025. To subscribe and download the magazine, click here: https://www.worldcement.com/magazine/world-cement/register/ )
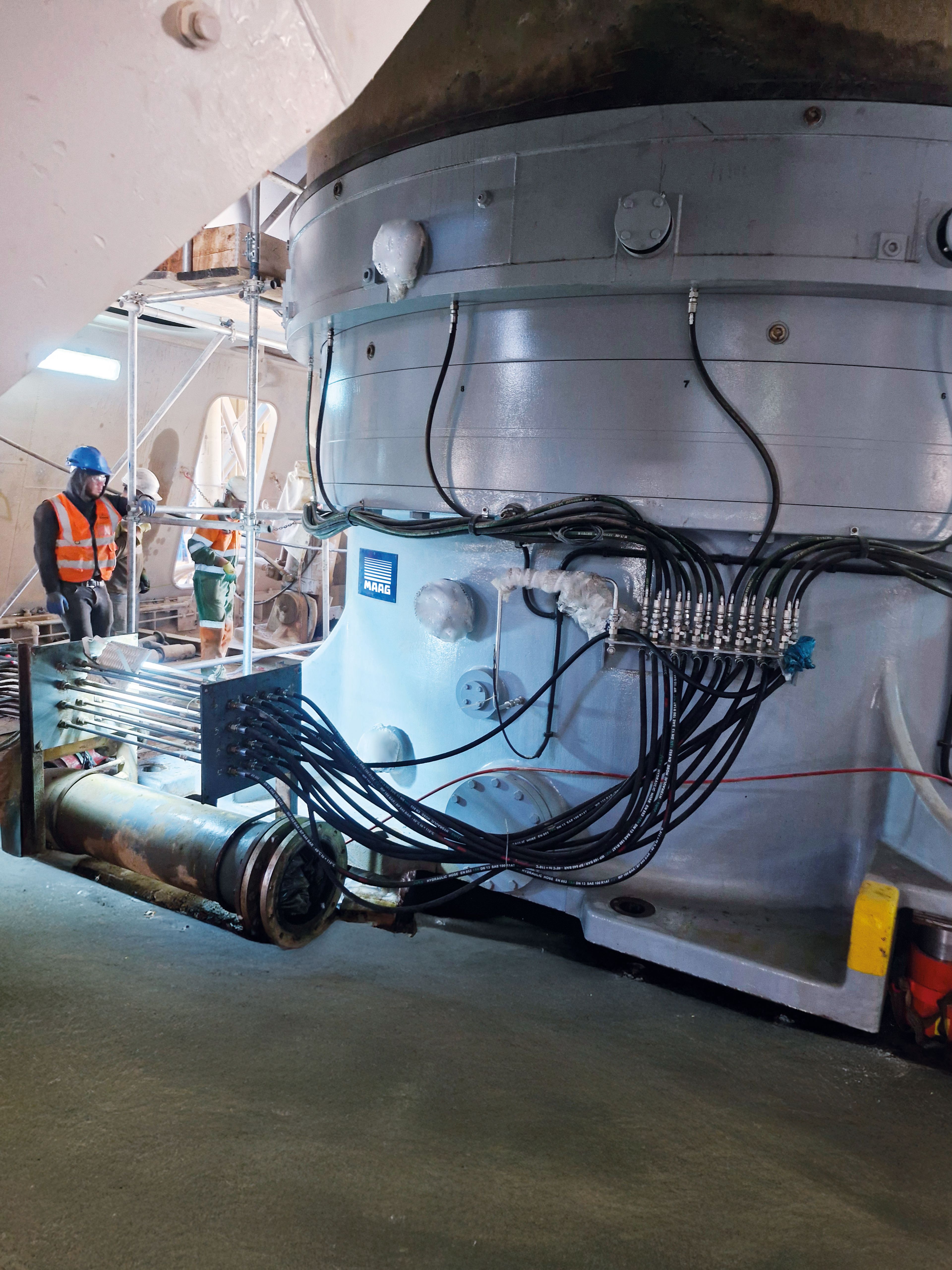
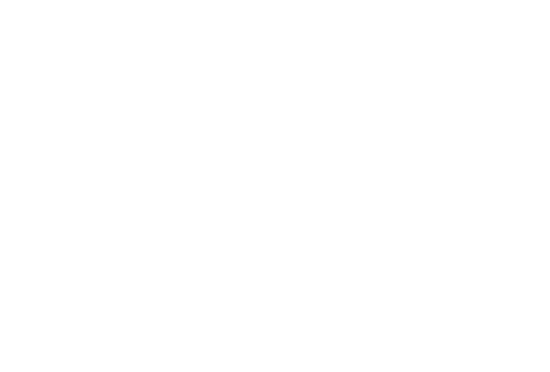
Join our newsletter.
Don’t miss out on the latest news, updates,
and insights - from MAAG.
© copyright MAAG Gear 2025. All rights reserved.
MAAG GEAR
INDUSTRIES
SERVICE CENTER
INDUSTRIES
SERVICE CENTER