Gearbox test run: ensuring reliability and performance
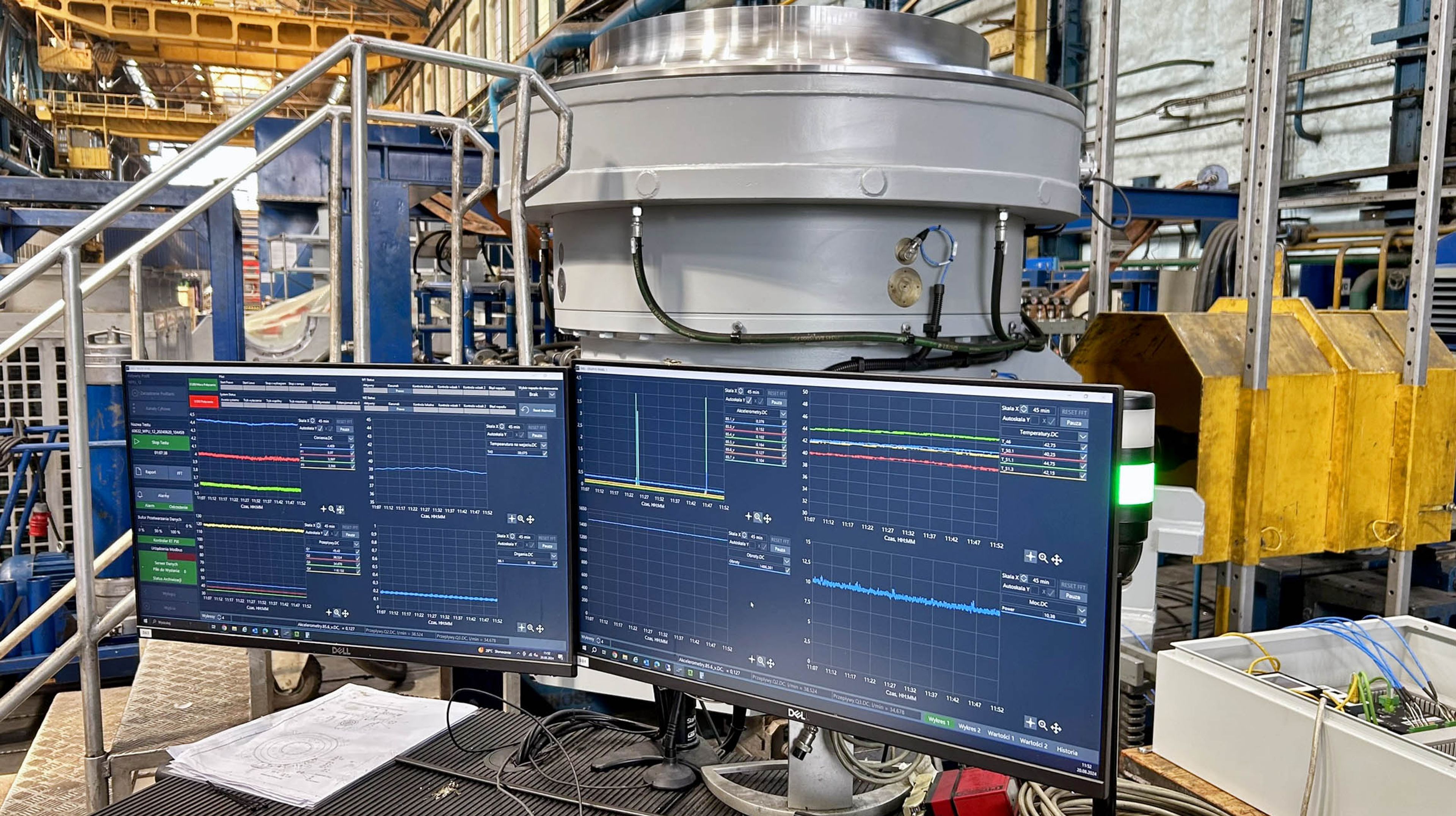
At our workshop, every gearbox undergoes a rigorous test run to ensure it meets the highest standards of performance and reliability.
Today, let's dive into the details of the test run process for the WPU-12/TS1 gearbox.
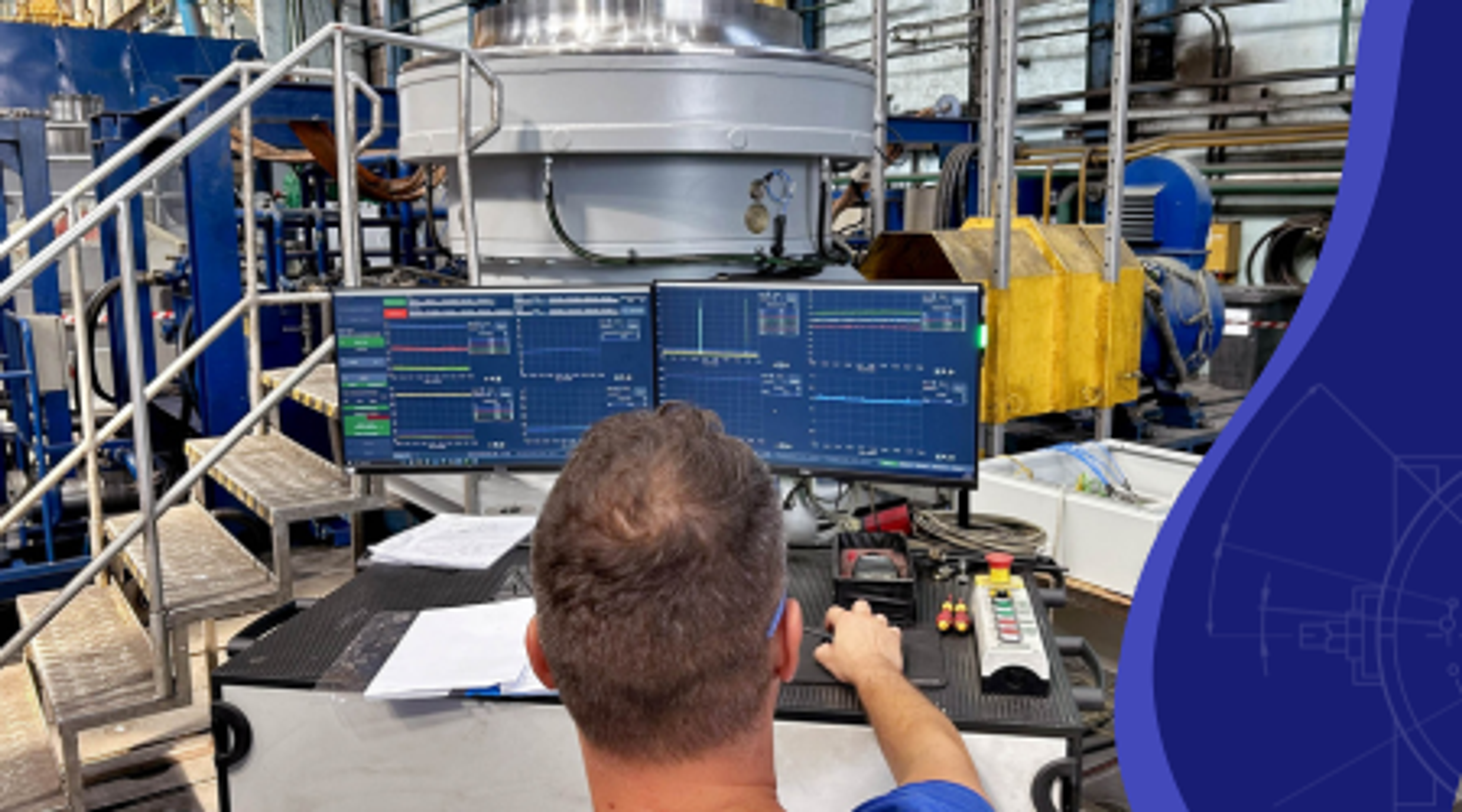
Key Testing Parameters for the WPU-12/TS1 Gearbox
During the test run, we carefully monitor and record multiple critical parameters
Oil Inlet and Outlet Temperature: monitoring these temperatures ensures the cooling system is functioning correctly, and that the gearbox is adequately lubricated.
Bearing Temperatures: Axial Thrust Bearing - Roller Bearings - Temperature control is crucial to prevent overheating and ensure smooth operation of the bearings, which are critical for load distribution and reducing friction.
Oil Flow, Distribution, and Pressure: proper oil flow and pressure are essential for maintaining lubrication and preventing metal-to-metal contact, reducing wear and tear.
Vibrations: measuring vibration levels helps identify any bearing problems, imbalance or misalignment in the gearbox components, which can lead to premature failure.
Input Speed: verifying that the input speed matches the design specifications ensures that the gearbox will operate efficiently when integrated with the motor.
Power Loss: calculating power loss helps in understanding the efficiency of the gearbox and identifying any areas of improvement in energy transmission.
Dynamic and Static Oil Film Thickness: this measurement is vital for evaluating the lubrication quality between moving parts (thrust pads and output disc) and preventing direct surface contact.
Run-Out of Connecting Flange: checking the run-out ensures the alignment and precision of the gearbox assembly, crucial for minimizing vibration and wear.
Run-Down Time: measuring how long the gearbox takes to come to a complete stop after shutdown helps assess the internal friction and condition of the components.
Test conditions for accuracy and consistency:
The gearbox undergoes a full-speed, no-load test for 2 hours to simulate real-world operating conditions.
Driven by a variable-speed electrical DC motor, we can precisely control and measure the gearbox's response to different speeds.
The test uses a workshop lube oil unit with ISO VG 220 VCI oil to ensure proper lubrication.
Lube oil pressure is maintained at a minimum of 2.8 bar (low pressure) and 10 bar (high pressure) to simulate various operating scenarios.
Oil flow rate is kept at 140 l/min under low pressure to ensure optimal lubrication throughout the system.
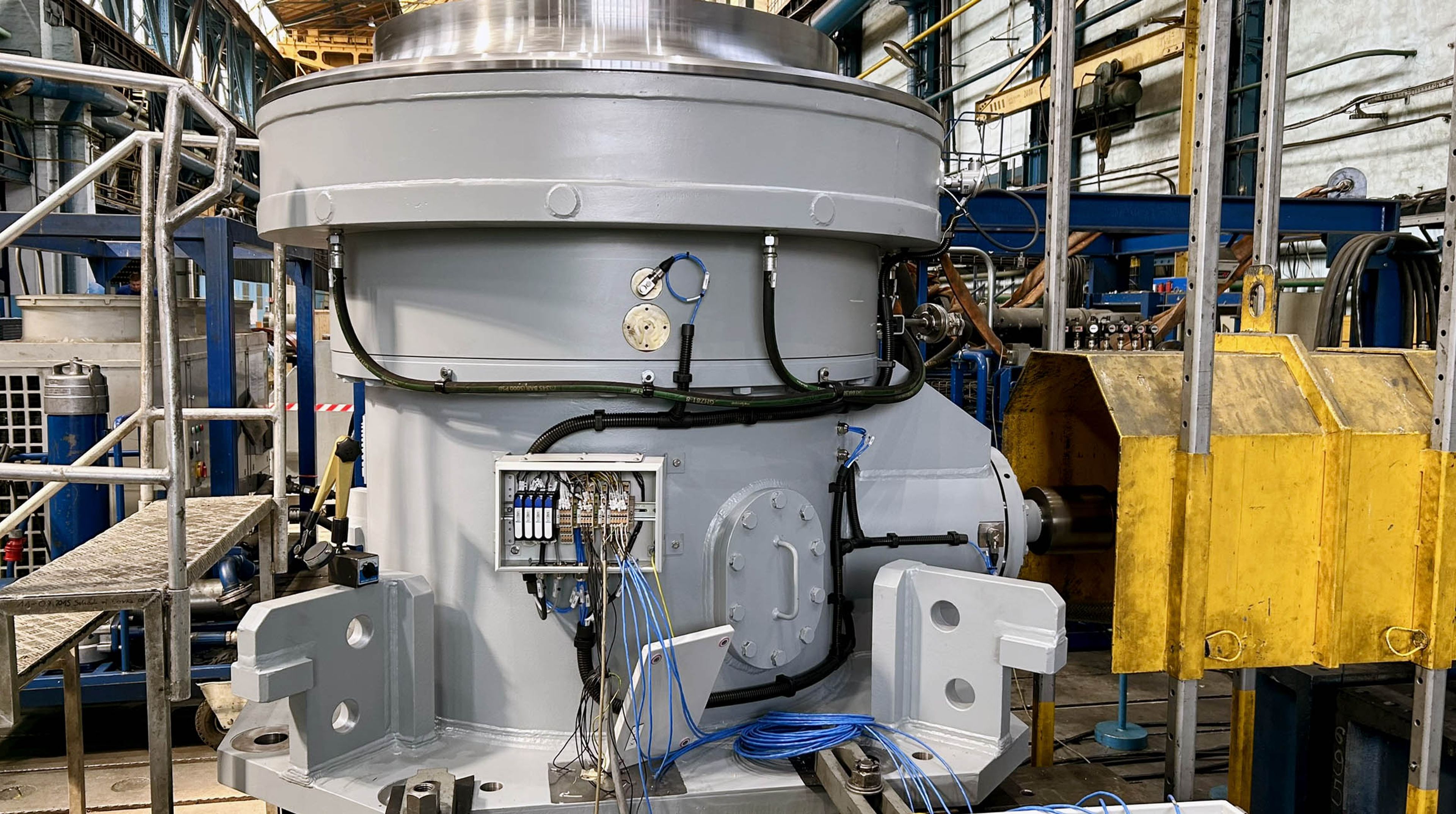
Tomasz Banasiewicz
Production Manager Assembly,
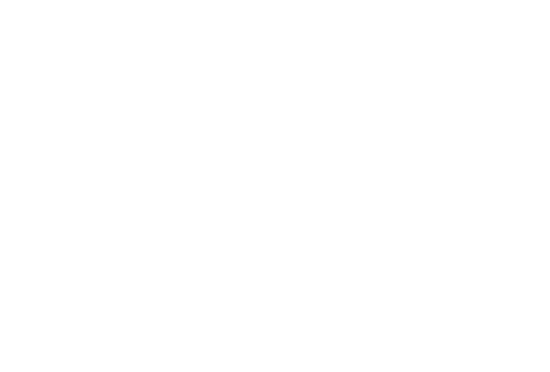
Join our newsletter.
Don’t miss out on the latest news, updates,
and insights - from MAAG.
© copyright MAAG Gear 2025. All rights reserved.
MAAG GEAR
INDUSTRIES
SERVICE CENTER
INDUSTRIES
SERVICE CENTER